The first step is taking apart the old house, so the foundation can be expanded and the new house built on top of the new and old. The owner has been posting a non-stop stream of photos on their project blog, and we've loaded them in a photo browser for you here.
Sabtu, 20 November 2010
Jumat, 19 November 2010
Small is beautiful and full of big potential
I really never post anything about the unbuilt, (oh . . . that sounds a bit like "the undead". . .), but I came across these cabin models on the D'Arcy Jones website which look so enticing and full of promise. – GF
Kamis, 18 November 2010
Tentang Mahal-Murahnya Fee Arsitek
Sumber
PreFab is Dead - the staggering FAIL of US Housing
As we enter Day 18 of my expo of Swedish Factory Houses on the LamiDesign Idea Log I can barely contain the magnitude of my outrage. I had to write this blog post simply to stop myself from going to the window of my studio, sticking my head out of the opening and screaming "I'm mad as Hell and I'm not going to take it anymore!" You have to understand the staggering, colossal, and tragic scale of the FAIL of the US Housing Industry to serve its customers.
So here is the deal. Sweden, a small country with the population of NJ, the size of California, manages to offer within its limited market dozens, I'll wager hundreds of modern house designs to its customers. And its not like each home builder has one or two token modern houses in the catalog. They all have a dozen or more. Even if you are part of that smaller margin that likes a modern house, you still have choice of dozens of houses where ever you might look to build a house. Yet here in the USA our corresponding mainstream home builders offer none. Nothing. Nada. Something is clearly wrong here. Our home builders say "if its not what most people want, then I won't offer it." In Sweden the mantra is completely reversed: "if its something that somebody will want, then we'll certainly offer it."
It makes some sense. Why bother to engineer the house and produce marketing material for a design that won't sell as well? Truthfully, that is not the reason. These costs are minimal, earned back in a single home build as the Swedes clearly demonstrate. The reason is because the American home builders can not build these houses as profitably as their mainstream offerings. Their carpenters in the field building repetitive houses get into a flow of their work, the dimensions and layout of the standard plans in a subdivision eventually committed to memory. They may use different siding on each one or a different facade treatment, but the houses are from a limited group of plans and the framing work is equal. How can they introduce into that work flow one or two modern homes with different plans and different massing without breaking their pace. Those one or two homes will take them longer to build, and will make less profit. Why even offer them? They don't.
Lets have a look at a Swedish subdivision. The houses here are all being built by Sävsjö Trähus whose designs we've just been posting in the idea log. Scott Hedges pointed this out. He writes:
This web page shows 5 houses built by Sävsjö Trähus all sold out of the Solna office. Solna is a really nice suburb of Stockholm where Ericsson is HQ (also where Skanska is) - these are all examples of the kind of houses that would be built by wealthy Swedes, executives in these companies.
Each of these was made by the same crew of guys in central småland. Each built, loaded, and shipped in a few days each, as part of a serial production of around 100 house packages like this a year. Not a lot of sophisticated automation or fixed systems, just teamwork and good planning. All built on their flexible little flip table in central smalland and carted up to suburban stockholm.
They could care less what style or kind of house they build. They just want it to be what you want and be affordable. Severe modern, ultra traditional, mildly traditional, mildly modern ... it just doesn't matter. They have every possible style of house that is reasonable for people to build.
Sign here. We'll send the permit drawings, and ship the whole house in a few weeks.
so you see nice traditional Swedish vernacular like this above, but you also see their functional modern style like this below:
No problem. Why wouldn't you do this if you could. Well they can. This is MMC and OSM. This is what it is capable of. Each of these homes was just as profitable as the next, because their process is geared up to serve the customer what they want. It is style neutral and value bias - whatever builds the most value for the customer leads the process. Forcing a buyer who wants a modern house to choose a traditional house clearly does not build value for that customer.
Are you mad? Are you ready yet, ready to not take it anymore?
Rabu, 17 November 2010
Selasa, 16 November 2010
MoTrad House - a new local client build
I don't often share projects from my local clients, unless they are modern or they have some connection to our Modern House Plans. In this case the project is a local build in Pennsylvania just outside Philadelphia. Its technically a renovation, but in truth is starting at the ground floor and rebuilding from there up, and adding to the back of the house. The new design shares a lot of DNA with the XHouse3 house plan, which is why we are going to watch the construction here.
Above and below is the existing house. A masonry one story houses, with a cape cod like proportion. One and a half story you would call it, as there are a couple of bedrooms under the rafters on the second floor. It has a companion detached garage to the rear, and its on a corner lot. Most of the house's neighbors are taller, with greater stature, so part of the brief was to give the house more presence. Owner also wanted the house to be compatible with the neighbors at the front, but modern in the back. Sounds like a job for a MoTrad Stealth house!
And this is what the house will be transformed into. In front the house respects the geometry of the existing historic homes, the Cape Cod roots of the house even more evident now. Yet the house and its dog-house shaped dormers will have a stark minimalism to their detailing.
In plan the house has much in common with the XHouse3, although the scale is slightly larger here. A centrally located stair takes you up to the bedroom level, and another short stair takes you up to the Master Bedroom level. Another couple of feet above the second floor, it affords the main living spaces a high ceiling.
The owner spent a lot of time getting to this point. Several other architects were engaged and ejected before we set to work on the design. He traveled to modern home tours in California and Atlanta all to collect ideas and take pictures of modern home inspirations. We worked through the schematic design, and advised as he applied his engineering background to preparing the construction drawings himself.
Here you see a section through the core of the house where an atrium extends up to the attic level above. This chimney ventilation will aid in venting warm air in the summer.
More images of the house design can be seen on our web site. The owner is self contracting, so we expect the pace to be slower than a full time gig, but follow along. It should be fun to watch this come together.
Menata Interior Kamar Tidur
Menata kamar tidur tidak pernah terlepas dari tata pencahayaan, tempat tidur jangan terlalu dekat dengan jendela, meskipun saat bangun tidur memang menyenangkan menghirup udara segar namun cahaya yang masuk disela-sela gordin dapat mengganggu kenyamanan tidur anda, sebaiknya diberi jarak antara tempat tidur dengan jendela.
Pemilihan warna tempat tidur, sprei dan karpet juga sangat mempengaruhi kenyamanan si pengguna, di hotel atau apartemen pemilihan warna ini sangat diperhatikan karena mereka mengerti pentingnya pemilihan warna ini, warna yang lembut dapat membantu releksasi pikiran yang lelah setelah beraktifitas seharian dan membantu untuk istirahat dengan tenang.
Ventilasi yang baik juga harus diatur agar saat tidur udara yang masuk dan keluar bisa teratur dengan baik, pernafasan saat sedang tidur dan beraktifitas sangat berbeda, nafas saat tidur biasanya akan lebih lembut, oleh karena itu harus disuplai dengan oksigen yang segar.
Untuk orang yang suka mendengarkan musik, sebaiknya diberikan speaker aktif di sudut-sudut ruangan agar saat tidur bisa terlelap sambil mendengarkan musik yang disukainya, mendengarkan musik sambil tidur juga termasuk terapi relaksasi terutama untuk orang yang memiliki kesibukan cukup tinggi.
Sumber
Terang dengan Cahaya Alami di Ruang Baca
![]() |
iDEA/Dean Martin Saerang |
Faktor yang paling penting dalam membangun suasana yang nyaman di ruang baca adalah cahaya.
Aktivitas membaca membutuhkan tingkat keterangan dengan iluminasi yang relatif tinggi. Pada umumnya yang dibutuhkan untuk membaca buku dan majalah adalah sekitar 400 lux. Kurangnya cahaya membuat aktivitas membaca akan terganggu. Selain itu, kekurangan tersebut dapat menyebabkan kerusakan pada mata.
Cahaya untuk ruang baca bisa diperoleh melalui pencahayaan alami dari matahari. Hal ini tentunya lebih menghemat konsumsi listrik Anda. Cahaya matahari bisa dimasukkan dengan membuat bukaan yang cukup lebar di ruang baca.
Contoh ruang baca yang baik misalnya memiliki jendela yang lebar di bagian depan meja baca. Jendela yang lebar ini memberikan kesan lapang pada ruangan. Pemandangan melalui jendela ke arah kolam renang memberikan suguhan yang menarik. Aktivitas membaca pun lebih nyaman ketika sejenak mata berelaksasi dengan pemandangan kolam renang.
Anda bisa menambahkan tirai untuk mengurangi intensitas cahaya matahari yang berlebih. Posisi jendela harus Anda perhatikan sebelum membuat jendela yang lebar untuk ruang baca. Hindarilah meletakkan jendela di barat. Cahaya matahari dari arah barat menyilaukan dan tidak baik untuk mata.
Sumber
Jumat, 12 November 2010
Nothing to dislike about it

The firm Three Fold Architects reinvented The Apprentice Store, which was an ancillary building to the adjacent DeMontalt Mill near Bath, England, which had been added to over 200 years evolving into 4 conjoined buildings, into a home.
There really nothing I don't like about this. The materials are so well mixed and considered, there's really nothing harsh or brutal that belies its former incarnation. Jump over to Dezeen and read it there. – GF
(the bottom photo doesn't really explain anything about the building, but I just love it!)
Kamis, 11 November 2010
Coming In From the Cold - the story behind the story or How the nations top scientists gave up on US home builders
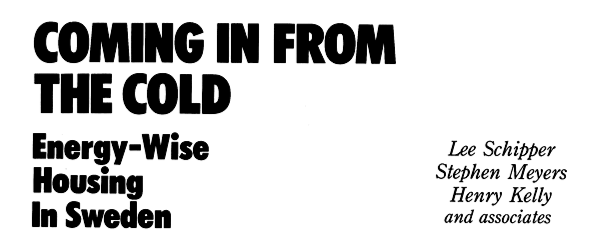
During the 1980's scientists working at the Lawrence Berkley Energy lab noticed that less energy was being used to heat homes in Sweden than in other industrial countries. Was the data wrong? No, Sweden was outperforming other countries. A man named Henry Kelly, who was director of a group called American Council for an Energy Efficient Economy, along with a Berkley scientist Lee Schipper, and colleague Stephen Myers, realized that the Swedes weren’t just building a few energy efficient houses. Rather they had managed to make the average house, the kind built every day much more energy efficient. The Swedes had changed housing though a comprehensive effort encompassing the building products industry, the construction industry, national building codes, national lending practices, and trades unions.
The USA had just passed through a severe energy crisis that rocked the entire economy. Our band of researchers saw what this could mean to energy policy in the USA. Determined to quantify the progress in Sweden, they secured a grant from the German Marshall Fund and cooperation from the Swedish Council for Building Research to do something that is rarely (if ever) undertaken by the building industry: an international collaborative study to find out what actually went on in Sweden and how it might inform the way we build and structure our housing industry here in the US. Their report was done in 1985 and the results distilled into a small book called Coming In From the Cold: Energy-Wise Housing In Sweden.
This book is the story of what they discovered. It documented the progress and results of the change to housing in Sweden and how the various factors in research, building, manufacturing, lending, codes, and oversight all contributed to the change. The book is a gospel for learning from the Swedish Housing industry. Its all in there, and it was communicated to congress and the National Homebuilders Association and anyone who would listen. Anybody with half a mind and this short booklet at their side could reshape the industry in a heart beat. A few thin pages could show the way forward to improve the quality of our construction, reduce energy use nationwide, and extend the benefit to anybody who wished to buy a home. They truly stood at the precipice of a new American housing industry.

Today, Lee Schipper is an internationally recognized expert on energy in transportation, and a co-recipient for a Nobel prize in climate change. His experience trying to convince American homebuilders to see the benefits of MMC and OSM left him feeling that they were hopeless to change. Schipper is still skeptical of the capacity for change in the homebuilding industry, saying recently "Swedes build good shelter, we build Tax Shelter".

The impressive careers of these two men, who have been honored for their work in every field except the building industry who ignored them, only highlights the tragedy that their work on Swedish housing does not grace their credentials today. Their revolution in American housing is glaring in its absence. The very people who stood to gain from these insights turned their back. The scientists went on to earn respect in other fields where science is valued. Meanwhile the NAHB gave the world the McMansion and went on to make a living lobbying against the kinds of policy innovation that led to Sweden’s success. And we know all too vividly exactly where that ended up taking us.
So here we are, 30 years later, and while I would be the first one to point out that the homebuilding industry in the US is largely the same as when Schipper and Kelly wrote Coming In From the Cold, the fact is that there are now greater pressures to change than there have ever been. The Passive House movement has clearly taken hold in the US. Energy performance is becoming a priority, and work weatherizing older buildings is seen as a way to both put people to work and help the nation's energy policy. Despite our progress in energy codes nothing points a clearer way forward than their book's recommendations. Residential lending in the USA, now clearly in a shambles, would also benefit from the lessons they've spelled out. Their book shows the way lending can be used to facilitate change in the industry, a tool for better housing rather than an out of control financial medium. And now as the housing industry is saddled with unsold and cheaply built oversized homes, its clear that a new kind of home, energy efficient, rapidly built, and smartly financed could put this housing industry back on its feet. Clearly there is demand for this new kind of home that the industry never got around to building. The kind of home that so long ago Kelly and Schipper showed them how to make. The emergence today of skilled and innovative builders like Bensonwood is validation of their prescient work done 30 years ago in Stockholm.
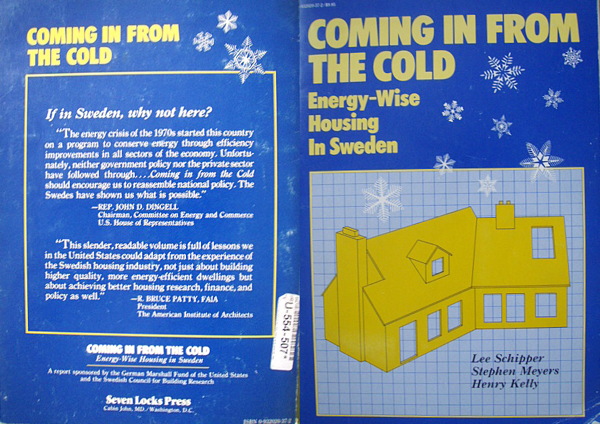
Minggu, 07 November 2010
Greg Lavardera's Modern House Plans + Bensonwood
All week we've been talking about factory house building in Sweden, and American timberframer and house manufacturer Bensonwood. The good news is that Bensonwood has begun to offer our house designs in their energy efficient building systems. The first house to be offered is the XHouse2.
We went through a detailed redesign of the XHouse2 with Bensonwood's engineering staff in preparation for this offering. The Bensonwood version of the house is subtly different on the outside. The front porch and rear deck framing is updated to be built with their timber-framing prowess. The wood cladding on the house reflects the products they have incorporated into their material stream. Internally the framing and details are completely revised to be built with factory made wall panels for a tight and energy efficient house. So although the design is clearly the same house, this is a unique edition you might say, only available through Bensonwood. Our house plan version remains designed for generic construction methods for the widest possible suitability. In fact its this generalized nature of my designs that allow them to be so readily adapted to Bensonwood's systems.
We're very excited to be able to offer our designs with such a high performance building system. Now you will find a new house plan group on our site for Bensonwood offerings, and the dedicated catalog page for the Bensonwood version of the XHouse2. From that catalog page you can click over to their site and land at their XHouse2 page.
Bensonwood will offer packages in different stages of completion from fully finished panels in their high performance Open-Built® format, to open framed panels only. This is a first step, although admittedly a small step, towards establishing a foothold for these new MMC/OSM manufacturing methods in the US. Look for us to expand the influence of these techniques in the future.
Kamis, 04 November 2010
PreFab is Dead - When can we expect MMC/OSM?
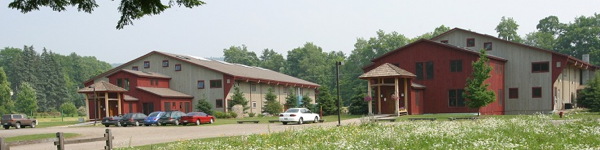
There are a number of US builders that have imported the various machines that are like the ones used in Sweden and in Germany, and they have used them for fabricating houses in panels - panelization as its called. But these builders do not attempt to finish their walls on both sides. Few even attempt to finish them on one side. Hence much of the great advantage of the technique is lost as a great deal of the work is still sent out to the field. There have even been attempts to import houses from Sweden, shipping them in their flat panel form to be assembled here in the States. A small quantity of houses were built and sold, but the designs of the Swedish houses admittedly did not make a clean fit to American expectations. For the most part the American housing industry has ignored Sweden's great achievement. A government funded report on the Swedish housing industry from the 1980s called "In From the Cold" documented the progress and results of the change to housing in Sweden. They presented this as a model for the US industry to follow, and then it largely fell on deaf ears. The researchers that conducted the study and wrote the report threw up their arms and moved on to other research topics. The few that have taken up some of these lessons have never carried them very far into the building process. They've done open panels, little more.
Bensonwood's journey into this was somewhat different. Coming from the American timber framing craft, Tedd Benson was quick to adopt computer driven milling equipment that he saw being used in Germany. This led him into the other types of automated fabrication techniques that were being used there, as well as leading him to be being present for the birth of the Passive House movement in Germany. Benson has been steadily taking this technology and the lessons of how they were building back to his shop in New Hampshire and evolving the way he builds homes here in the States. He's faced the same stumbling blocks that we've reviewed in examining the Swedish factory. Our building products here don't help you to panelize your walls, never mind make a high performance home. So along the way Bensonwood has been diligently adapting American products, importing european products where practical, and inventing what was missing, all in the pursuit of an intelligent manufacturing process. There is that word again! Intelligent! They have been connecting the dots where American component suppliers fail to, and building more and more value into their product. This is their form of MMC and OSM.
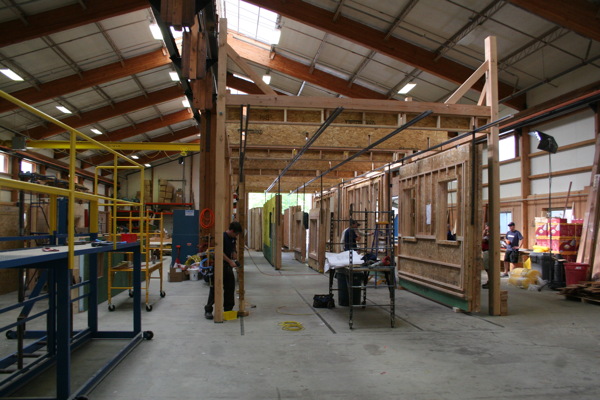
So where are they? Right now Bensonwood has several standardized wall and roof construction models that they can use to build a wide range of typical Amercian homes. Basically, if a home can be stud framed, then the Bensonwood system can be used to build that house. The system is offered in different degrees of insulation value to suit your climate, but it is worth noting that these can be used to build a home to a Passive House level of performance. Bensonwood calls their system Open-Built® and it supports the core philosophy of how they approach building homes. Number one the system is capable of very high energy performance. Number two it is configured for separation of utilities and structure, which allows the changes that happen over the life of a home to go on without interfering with the structure or spoiling the air tight envelope of the house. This supports Bensonwood's belief that a home should be built to last for generations.
The reasoning of Swedish factory builders is not precisely the same, but the prototypical wall construction in Sweden is very similar. Consistently they create an interior side chase space inside of the homes vapor barrier that allows wires, switch boxes, and plumbing to go where needed without puncturing the airtight envelope of the house. Bensonwood's Open-Built is the only thing approaching this offered in the US. There simply is no "PreFab" house that takes this deep approach to building science and performance offered in the US.
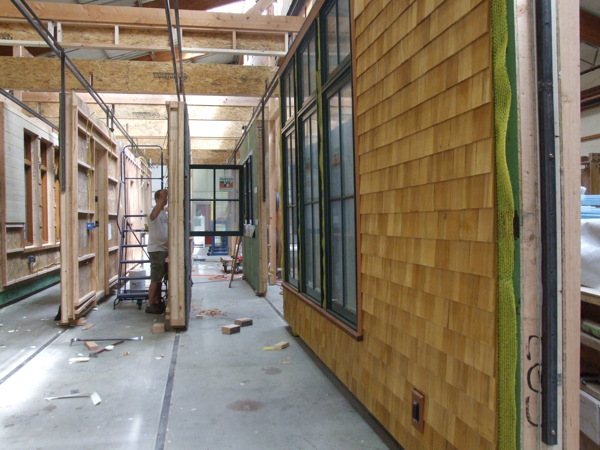
Bensonwood is also building with largely finished wall panels as the Swedes are, although they continue to offer partially finished packages for US builders that choose to finish the work themselves. However Bensonwood currently works their panels in a vertical orientation using a unique racking station that they've created themselves. Whether they transition to flat work like the Swedes remains to be seen. The process is ever evolving and there is always more to learn. The materials and finishes offered by Bensonwood reflect their New England roots, and as such the selections are extremely high quality and consistent with the high quality of their product.
We are excited to begin offering our house designs through Bensonwood, built to their high standards. We believe this opens up an entire new opportunity to our customers who are very interested in energy performance and the concerns of a sustainable and green home owner. Up till now the only option for people who liked our designs were our house plans. Out of necessity these are very generalized when it comes to performance. They are designed to use the most common construction materials, to make them easy to build, and build-able over the greatest range of locations. Bensonwood's offering opens up a new market for those interested in our designs, but seeking the best performance they can get. The universality of our designs make them readily adaptable to Bensonwood's building systems. We are really looking forward to seeing them build your LamiDesign modern house.
Selasa, 02 November 2010
PreFab is Dead - Long live MMC and OSM
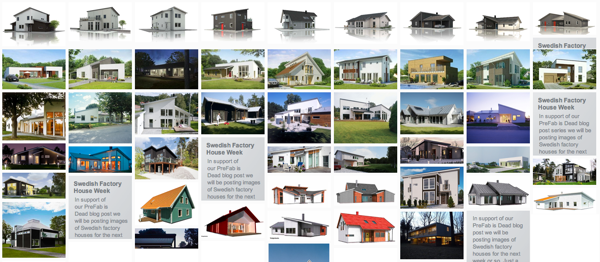
So what happened in Sweden? We've gone over many of the details of how their building practices differ in prior posts. But what happened that enabled them to get to this point? In our LamiDesign Idea Log we've been posting images of Swedish Catalog House designs that are Modern. We've posted dozens so far, and there are more and more and more to show. How is it that a small country like Sweden can offer such a range to a market of limited demand like Modern? Yet here in the USA our larger merchant builders can offer none? Even if the percentage of buyers interested in modern in the USA is less than in Sweden, if you added them all up it would be larger than the entire market for the whole of Sweden. Yet our builders here can't even address this market with a single viable product? Not one modern house offered by the big builders that represent the majority of our market. Can you grasp the enormity of this failure?
In the late 60s and early 70s energy prices were rising worldwide. Sweden made a holistic overhaul of their building practices at this time to raise the energy efficiency of the homes they were building. There was cooperation between builders, labor, manufacturers, and the government to make this happen in a short amount of time. The results of the effort are impessive. Imagine that the winter climate in Sweden is much like Maine or other northern states. Yet the homes built in Sweden use less than half the energy of homes built in the US. They don't do this by turning down the thermostat, or curtailing the area of the home they heat. They have higher indoor temperature expectations than we do, and still they use less energy. Homes in Sweden are not viewed as stepping stones to bigger homes. While this remains a cultural difference between our countries, it gives them a commitment to make each home of high quality, including its energy performance. Prior to this push Swedish homes were built with wall construction of R18, and ceilings/roofs of R24, not too far from what we produce in the USA today. But today in Sweden standard walls are in excess of R30 and ceilings/roofs in excess of R40, and these gains were led by the industry and by market demand - not by building codes.
The factory building practice in Sweden has been driven partly by their short building season, but also by the gains in efficiency that have been developed in their factories. Housing is treated as a product, and as such every aspect of the design is rationalized into a know quantity of work, material, and ultimately a known price that is both profitable and viable in their market. During the time their industry was reinventing itself the various products and fittings that go into a house were all revised, improved, and updated to integrate into this industrialized process. Contrast this with our country where almost every home is built as a unique event on each site. Some industrialized components go into them, but for the most part each house is custom built even when the house next door is identical. Yet Sweden can offer its customers a more "custom" home buying experience than US consumers have. The computer driven fabrication tools they use give them great flexibility in their offerings. In the US if a buyer wanted a modern house in a development, the crews would have to reorient themselves to a new house design, building it once, and losing any speed they gained from the repetitive houses on other lots. That modern house of the same size will cost that builder more to build, and it will take longer too. They simply won't do it. In Sweden all they need to do is roll out the digital files for the requested design and set in motion the process to build the customer that modern house. Same process as the other houses, and the same cost. Its Customer driven.
The level of flexibility inherent in the Swedish housing industry is just not present in our so called PreFab industry. A typical modular builder in Pennsylvania has moved the construction process indoors, yes. They've avoided weather, and gained the benefits of working in a central location. But they are still framing walls as they did in the field, building boxes, and completing them in a similar sequence as site building. Wall frames are tilted up into place, and ladders or scaffolds give the workers access to all the vertical work needed to complete the modules. Insulation, sheathing, cladding, drywall, all applied on the vertical, just like building in the field.
Lets contrast that with a typical Swedish process. We'll even look at a Swedish modular builder to emphasize the difference. Walls are quickly framed up by automated machines being driven by digital data. Sheathing and cutting out of the window openings again are all automated. Siding is applied by an automated machine as the wall panel rides down the line, and its even painted on the flat. Finally the entire wall panel, with drywall on the inside, painted siding on the outside, windows all installed, is lifted on to the floor panel to make the modules. Joints closed, and the interiors finished. But nobody was up and down a ladder until the modules were formed. The walls were done when they went vertical.
I'd like to continue to just be very instructive about this, but at this point one really has to ask what the hell we are doing here in the US. It seems we are playing prefab house building like so many children with cute tool belts around our waists. Meanwhile the Swedes have created an intelligent industrial process, one that builds houses with precision, that ensures a tight house and improves quality, and provides reliable cost and schedule while making a far superior product. This is a MODERN - as in it is driven by contemporary industrial techniques and processes - METHOD - meaning somebody has thought about what we are doing, and ways to remove waste and inefficiency from the process - of CONSTRUCTION - meaning in the end we arrive at a house, the same goal as PreFab, but so much more calculated and precise. This is OFF SITE MANUFACTURING - here it is important to distinguish this from construction. We are not doing off site construction, right, because the Modern Method of Construction is MANUFACTURING, not construction. Manufacturing takes forethought. It takes planning of process, and planning of material streams, and waste reduction. Its not just the dynamic of building the house, but the designing and implementation of the industrial process to build houses. This is why PreFab is Dead. This is why MMC and OSM are our future.
Holy Crap, that sounds difficult you say - we have no idea how to do that. Just let us take our hammers and ladders and go back to the construction site. No no no no. The amazing part is that somebody has already figured this out. We don't have to start from scratch. We don't have to reinvent the wheel because the Swedes have already done it.
--
A short addendum, just to look at the window installation from these two videos.
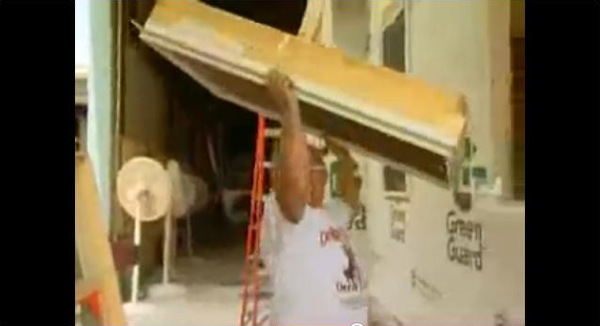
Here is our American friend hoisting his window into the window opening - his poor back! The wall is done, its already covered with house wrap. The window goes in from the outside, so he is reaching up over his head to put this in place. He'll be up the ladder in a few minutes to put a gang of screws through the "nail flange" of the window frame. There are no adjustments, you get it straight and screw it in. Later they will come back and put spray foam into the gap between the window and frame, or just stuff loose insulation into the gap.
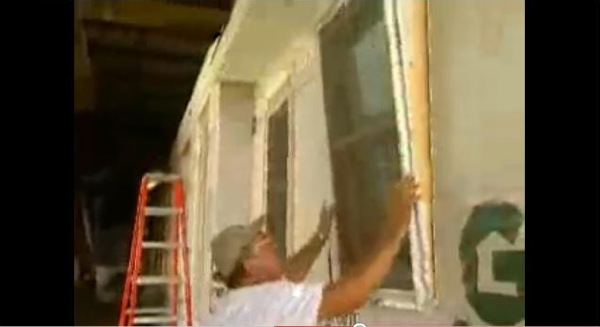
Its not this fellow's fault. This is the way windows are installed in the field, and its the only way mainstream residential windows are made in the USA. So lets look at our Swedish friend. He's working on a table, with all his tools around. He does not have to carry each window to its location - the work is basically coming to him.
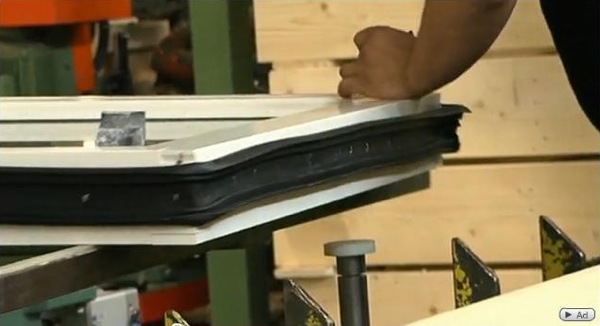
First he installs a butyl gasket all around the perimeter. No caulk gun or spray foam - this is a permanent gasket that will outlast any caulking or flashing tape. Then he installs the window into the framing - that's right - the window is installed before the wall is framed up. The assembly he is working with is the jamb studs, sill, and header, so he is able to square the opening before the opening is screwed into the entire house where if its crooked, its going to stay crooked. The studs and window are introduced into the wall framing at once just as the next stud down the wall. The Swedish window is mounted with six adjustable fasteners that allow the window to be adjusted once installed so even if there is any movement down the line it can be corrected - no call backs. This is analogous to the adjustments in cabinet hinges that allow you to square the door. Not only that, but the window can be easily replaced without tearing out subsequent work.
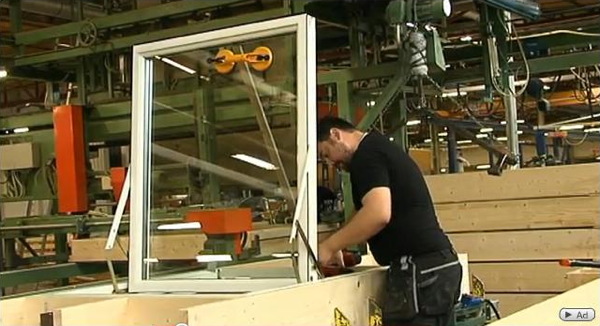
So our Swedish friend did not waste any time on a ladder. Nor did somebody have to comeback and seal up the window after it was installed. And its saved time down the road if the window needs to be adjusted, or replaced.
This is what we are getting at here with MMC/OSM. Every part anticipates its place in the overall assembly process. The American window at best has done a decent job of figuring out how to take their product and screw it to sh-t. You want to screw that baby down - we got you covered. You want us to seal that window for you, or let you adjust it if something got out of square, or make it easy to replace if somebody dropped a hammer on it. Well sorry bub, you are on your own there. These small steps not only save time in building the house, they improve quality, and they deliver more value to the customer. Get it?