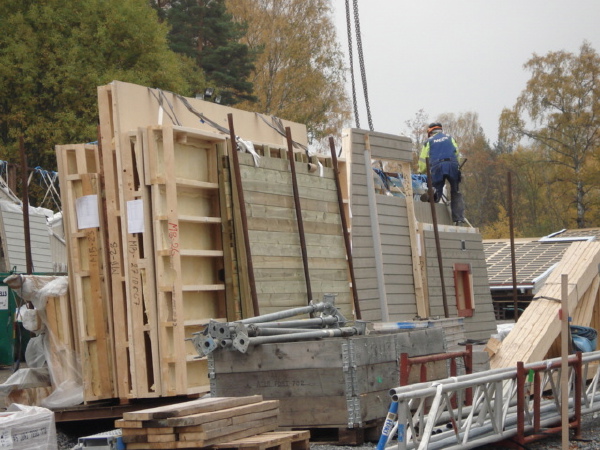
Click through below to continue reading..
Scott began by telling me about the typical process by which houses in Sweden are built:
"...the majority of new construction is built like this. I would call the house panelized - but it is "way way panelized" and is a total package. The houses come on trucks from rural places in Sweden. The windows are in, the insulation, wiring, wallboard where possible - every thing - the pipes, the wiring systems, the doors, stairs ... everything has been engineered and rationalized to reduce labor, find energy and material economy and work with the method of construction where stuff is pre-assembled as much as possible inside a building and then "erected" or installed on the site under very compressed schedules. These houses go from slab to dry in and locked inside of a week - the fit out and installation of everything else is really much like what I've seen in the USA - you just can't squeeze that much more out of what happens on a building site ... other than make it a total package and schedule the deliveries in the most rational way. For instance you have to install the interior ceilings after the house is up - however you can load the sheetrock in the room as the sub floors go down (and they do) which cuts down own lugging stuff around."
Lets contrast this with the US. There are some companies doing panelization, but typically it is only carried as far as the rough framing. Wall panels come to the site with studs framed and sheathing on. Its a short cut on rough framing, but the siding, insulation, utilities, and interior finishes still need to be added. The LV House is a good example of this. More recently the prototype Loblolly House has won awards for its integration of building systems into the panelization. But lo and behold - this is standard practice in Sweden. Wall panels come to the site with siding on the outside, wall board on the inside, and wiring and plumbing in place within the walls. Why can't we do that? One of the issues are our standard practices for electrical and plumbing work. They do not lend themselves to these field connections between adjacent panels, where as the Swedish standards are designed to ease these very conditions.
>
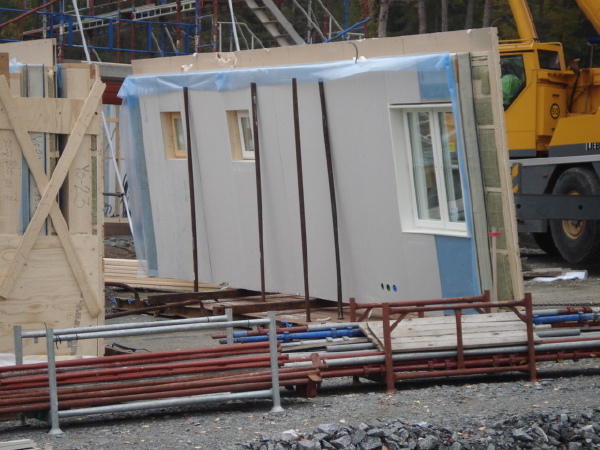
But the majority of prefab in the USA is in the form of modular construction. Modular construction reduces the field connections to a a few major utility connections when the boxes are placed on the foundation, but otherwise are much more complete when they arrive at the site. Granted, this is not the reason why modular is more popular in the US. Modular housing here grew out of motor-home construction, which was a more permanent version of a trailer. When the flimsy construction of motor-homes became an obvious problem in the US it was put under a nation wide spec known as a HUD Code. At that point the industry split into factories that continued to build motor homes under the new rules, and factories that adapted to building to local site built construction codes which became the modular industry. That has dominated the US prefab business ever since. Its popularity here is due to administration - not because it makes construction sense. And how could it make construction sense? Shipping a house in big pieces is tantamount to shipping air. There is a reason why Ikea ships furniture in a flat-pack. The shipping is so much more efficient for flat goods, than big boxy hollow goods. The challenge becomes how to complete as much of the house as possible while still being able to ship it flat. Whole houses arrive on two trucks rather than 4 or 5.
Next we'll get into more detail about how these houses go together.
Previously:
Letters from Sweden - conversations with an expatriate builder
Technorati Tags: modern design, modern house, prefab house
Tidak ada komentar:
Posting Komentar